Diesel vehicles can have one of the four types of injection pumps: rotary, in-line injection, continuous, and high-pressure common rail pump. But what is a rotary injection pump, and how is it better than the other three types of pumps?
In the world of diesel engines, we see rotary injection pumps as a notable innovation. That’s why we believe it is important for you to understand how they work and reveal their advantages and disadvantages. We will also list the components of rotary injection pumps so you can entirely understand their role.
What Is a Rotary Injection Pump?
The rotary injection pump got its name from its circular design. They were used on cars and light trucks when they were first invented. Today, they are applied to various diesel engines because of their durability and sustainability. Rotary injector pumps are also known under the name of distributor fuel injection pumps.
So, what is the function of a rotary pump engine?
As with every other injection pump in diesel vehicles, the purpose of the rotary injection is to deliver the correct amount of fuel to each cylinder. Their work requires high precision. The pump is responsible for delivering the fuel at the right time so it can be combusted.
Out of all the types, the distributor pump has the most compact and lightweight design. Hence, it is the best injection pump for vehicles that have limited space. At the same time, manufacturers avoid installing it on diesel engines with high capacities because of its design and capabilities.
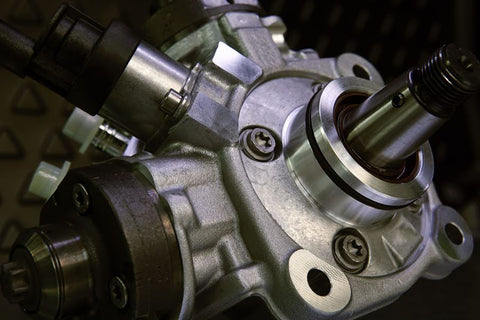
Source: shutterstock.com / Photo Contributor: Orlov Alexsandr
Types of distribution injection pumps
The distributor pumps can be divided into two categories according to the movements they make. The first type is the axial piston distributor type or VE for short. The VE-type pump moves in an axial direction so the piston can compress the fuel.
On the other hand, the radial piston, or VR-type pump, has several pistons that are laid out in a radial shape. Generally speaking, radial piston distributor pumps receive higher pressure compared to the one-axial piston.
Parts of Rotary Injection Pump and Working Principle
To fully understand what is rotary injection pump, you need to get familiar with its basic parts. The rotary injection pump has a rotor with two radial holes, which are located at different heights. The fuel inlet passage is on the bottom side, while the fuel outlet passage is on the top side of the rotor.
The rotor also has multiple vanes, which can also be called blades. This component of the injection pump is typically driven by an engine camshaft.
Inside the rotor, there is a longitudinal cavity for fuel. The pump operates by doing circular or rotary movements and has a single pumping element. How a rotary injection pump works is by distributing the fuel to every cylinder in the engine. The rotor turns allowing the pump to deliver the right amount of fuel in each cylinder.
The rotary injection pump also has one plunger and a spring in the middle. They are placed at the lower part of the rotor, and their job is to bring fuel into the cavity or force it out.
The reciprocation of the plungers is controlled by a cam ring. The internal surface of the cam ring has an almost square shape where the plungers rotate.
Other important components of a rotary injection pump are:
- Transfer pump and liner
- Vane pump
- Metering valve
- Solenoid shut-off valve
- Fuel adjustment plate screw
- Show roller assy
- Pumping piston plunger
- Governor weight
- Transfer pressure
- Delivery valve holder
How does a rotary injection pump work?
How a rotary injection pump works is that the plunger takes a rotating motion. The motion of the plunger is turned into a reciprocating motion as it uses the cam plate, which has several lobes. As a general rule, the cam plate has as many lobes as there are cylinders in the engine.
The fuel enters the distributor fuel injection pump through the inlet passage. It is typically drawn from the fuel filter. The fuel that is coming into the pump is regulated by the metering valve.
The pressure that the rotary injection pump works with varies according to the engine speed. As the rotor rotates, the inlet bore in the rotor aligns with the inlet bore in the pump head. As the rotors align, they are pushing the fuel from the cavity.
The distribution system distributes the fuel to each cylinder. The fuel is distributed in the firing order of the engine.
What Are the Advantages of Using a Rotary Injection Pump?
There are several advantages of a rotary fuel injection pump. We will start with the installation process. Because of their small size, they can be easily adapted to a variety of diesel engines. Plus, they can be adapted to add-on modules.
When it comes to the performance of the vehicle, rotary injection pumps bring several advantages to the table. In the diesel industry, we know them as pump types that have low fuel consumption and reduced toxic emissions while making less noise. Furthermore, they produce high injection pressures and have a high power-to-weight ratio.
Disadvantages of rotary injection pump on diesel car
Compared to any newer injection system, rotary injection pumps might have trouble with timing and delivery of the fuel. They are also limited in the power output they can deliver. Additionally, the rotary injection pump has limited compatibility when it comes to alternative fuels.
Signs of a Faulty Rotary Injection Pump
Although it has a simple design, the rotary injection pump might start to malfunction. If that happens, you might notice issues with your car. Some of the most common signs indicating that the rotary pump on your engine is faulty are:
- The engine is having a hard time starting
- There is no throttle control
- Sudden fuel leaks
- Fuel marks in the oil
- Plugged nozzle
- Seized head

Source: shutterstock.com / Photo Contributor: kanemme6