Fuel injection systems are crucial parts of the performance of modern vehicles. Diesel engines require fuel injection systems for fuel delivery. The engines cannot function without them, and the most popular systems are common rail diesel and direct injection. But what is the difference between common rail diesel vs direct injection?
Let’s dive in and explore the common rail vs direct injection differences as well as the benefits of each system!
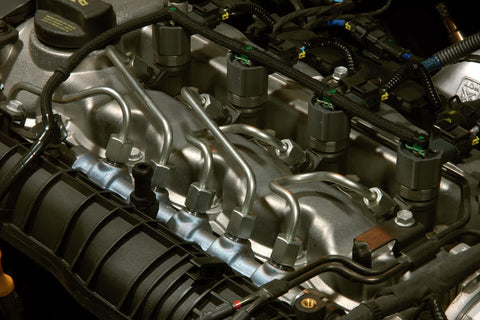
Source: shutterstock.com / Photo Contributor: algre
Common Rail Diesel vs Direct Injection
Diesel engine-powered vehicles need fuel injection systems to deliver fuel to the engine cylinders. Once the fuel reaches the engine cylinders, it mixes with air and ignites to produce power.
In diesel engines, fuel systems use a fuel injector pump to move the fuel. As mentioned, diesel fuel injection systems can be either common rail diesel or direct injection. Even though both injection systems are for diesel engines, they have several differences.
Both common rail diesel and direct injection fuel systems have advantages and drawbacks. Hence, it is good to compare them and see which is best suited to your diesel vehicle. Using the right diesel fuel system may significantly impact your
- Engine performance
- Fuel efficiency
- Emissions
Understanding direct injection (DI)
A direct injection fuel system is the classic option between the two. This system uses a mechanical pump to deliver fuel to the engine. The mechanical pump in the diesel injection system is the part that generates the pressure needed to inject fuel into the engine.
Despite its simple design, direct injection is still a reliable and cost-effective fuel system for diesel engines. Due to the direct injection being more affordable than common rail diesel, it is a popular choice for older diesel engines.
Historical evolution and development
Direct injection fuel systems were initially introduced with the first diesel engine in 1890. The historical injection system was known as “air-blast injection”. Since then, the direct injection system has undergone many improvements and developments.
The initial air-blast injection design was improved with a better-accumulating system. This allowed for a direct injection system without an enormous compressor.
Advantages of direct injection
- Improved fuel efficiency - Direct injection offers better fuel atomization (finer fuel spray), burning fuel more efficiently. This process leads to the affordability aspect of this system as it does not waste fuel.
- Enhanced engine power and performance - With a direct injection, diesel engines may experience increased engine power and performance due to the pressure. In terms of performance, it also reduces turbo lag.
- Reduced emissions - Another advantage of the better fuel automatization in direct injection systems is that it produces lower emissions.

Source: shutterstock.com / Photo Contributor: Alex Artx
Exploring common rail diesel (CRD)
A common rail diesel injection system is a contemporary fuel injection system that supplies pressurized fuel to the engine's injectors. This system uses a central rail in a separate electronic valve that controls each injector.
On the other hand, direct injection systems use mechanical pumps to deliver fuel straight into the combustion chamber, where it combines and ignites with air. Common rail injection systems outperform direct injection techniques in terms of efficiency and quietness by design.
CRD evolution and adoption
Common rail diesel injection is another type of direct fuel injection system that was first developed in 1916. The first application of the common rail fuel system was in submarines.
However, the first common rail diesel engine incorporated into a road vehicle was the MN 106 engine by East German VEB IFA Motorenwerke Nordhausen. Still, common rail diesel mass production didn’t happen until the mid-1990s.
Moreover, modern common rail diesel systems operate with an engine control unit. This unit opens each injector electrically instead of mechanically.
Advantages of common rail diesel
- Better fuel distribution and combustion - CDR provides better fuel distribution as the fuel spray is controlled electronically, allowing for better control. Plus, with the improved combustion, there is emission reduction.
- Higher torque and improved engine response - Provides up to 25% more torque than regular engines delivering the same amount of fuel.
- Lower noise levels - Due to the timing flexibility with common rail diesel, there is an excellent improvement in noise, vibration, and harshness.
Key Differences Between CRDi and DI
Fuel delivery mechanism
The primary difference between common rail diesel and direct injection is the method of fuel delivery. Direct injection systems use a mechanical pump to feed fuel to the engine.
Common rail diesel systems deliver fuel directly to the injectors electronically using high-pressure pumps. The 'rail,' a centralized high-pressure fuel pump, is used by common rail diesel engines to supply pressurized fuel to the injectors.
Performance comparison: CRDi vs direct injection
Fuel efficiency comparisons
Common rail diesel fuel systems have better fuel efficiency and performance than direct injection. This is because CRDi systems allow for multiple fuel injections per engine cycle. Since fuel is delivered to the individual injectors, CRDi maintains fuel at a consistent pressure, improving fuel efficiency.
Power output and torque differences
Direct injection systems use a mechanical pump to deliver fuel, meaning the power output is lower. In comparison, CRDi uses a high-pressure pump, allowing for greater power output and torque.
Emission levels and environmental impact
The high-pressure pump in CRDi fuel systems is electronically controlled, allowing even fuel dispersion. The consistent and controlled fuel delivery in CRDi systems makes them a more environmentally friendly option due to the lower emissions.
Application and Usage in the Automotive Industry
Different applications of CRD and DI in various vehicles
Direct injection systems are more affordable, making them a popular choice among customers. They are often used for cars with older diesel engines but are insufficient for heavy machinery.
In contrast, CRDi systems can provide more power. So, they are used in cars, trucks, and heavy machinery.
Industry trends and prospects
The automotive industry is always subject to improvements. For instance, technological advancements in fuel injection systems, like enhanced injection pressures and multiple fuel injections per cycle, improve CRDi systems’ performance.
This, in turn, drives up the inclusion of CRDi fuel systems in the industry. Another reason for the adoption of CRDi and DI systems is the rising popularity of diesel vehicles.
Therefore, fuel efficiency, reduced emissions, and better performance increase the demand for CRDi and DI injection systems. This trend of increased demand is expected to have substantial growth in the future.

Source: shutterstock.com / Photo Contributor: sima
Conclusion
There are several common rail diesel vs direct injection differences. Mainly, you can spot them in fuel efficiency, performance, and affordability. While direct injection systems are more affordable, CRDi fuel systems enhance fuel efficiency and better overall performance.